Can Crusher & Recycling Sorter
The final project for MEMS 1049 - Mechatronics, the can crusher & recycling sorter synthesized both mechanical and electrical design (living true to the definition of the class name). The project involved mechanical design in both the crushing gear train, lead screws, bearings, fixtures, and the machine frame. The control system and user interface utilized many electrical components (including microcontrollers, h-bridges, 7-segment displays, display driver chips, switches, and various passive components) to complete the system. Existing at the overlap between the two disciplines, mechatronics is a particular interest of mine and, I believe, a key component in the future of mechanical engineering.
The full mechanical and electrical systems were designed from scratch and manufactured in the Pitt Makerspace. I developed a fully parametric, equation based lead screw and nut generator in SolidWorks optimized for 3D printing these components. OnShape was utilized to design the double helical gears for the crushing motor. These parts, as well as hexagonal shaft connectors, tapered roller bearings, and conveyor rollers were 3D printed allowing for rapid prototyping and low-cost manufacturing. Frame components utilized the x-carve CNC routers after initial prototyping using laser cut cardboard. The laser cutter was also used to make breadboard mounting panels, mounted on the reused PVC support pillars.
The electronic design was based around the ATmega328P running C programs. Three controllers were utilized for crushing motor, conveyor motor, and seven-segment display. The controllers utilized binary and SPI to communicate. DC motors were used for both the crusher and the conveyor, with motor analysis completed to ensure proper motor sizing. The final circuit was build on breadboards and a CAD schematic was built for final documentation.
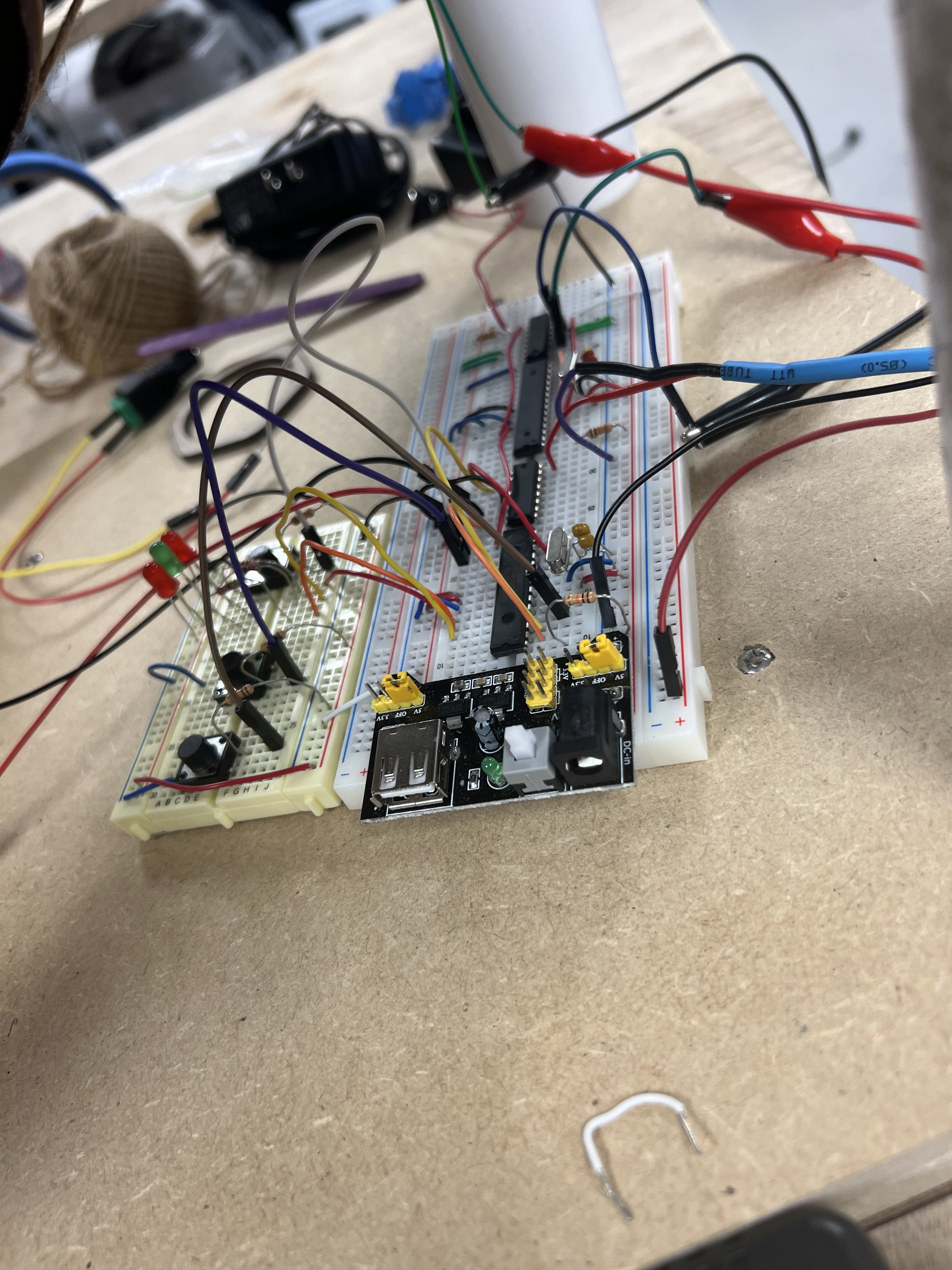
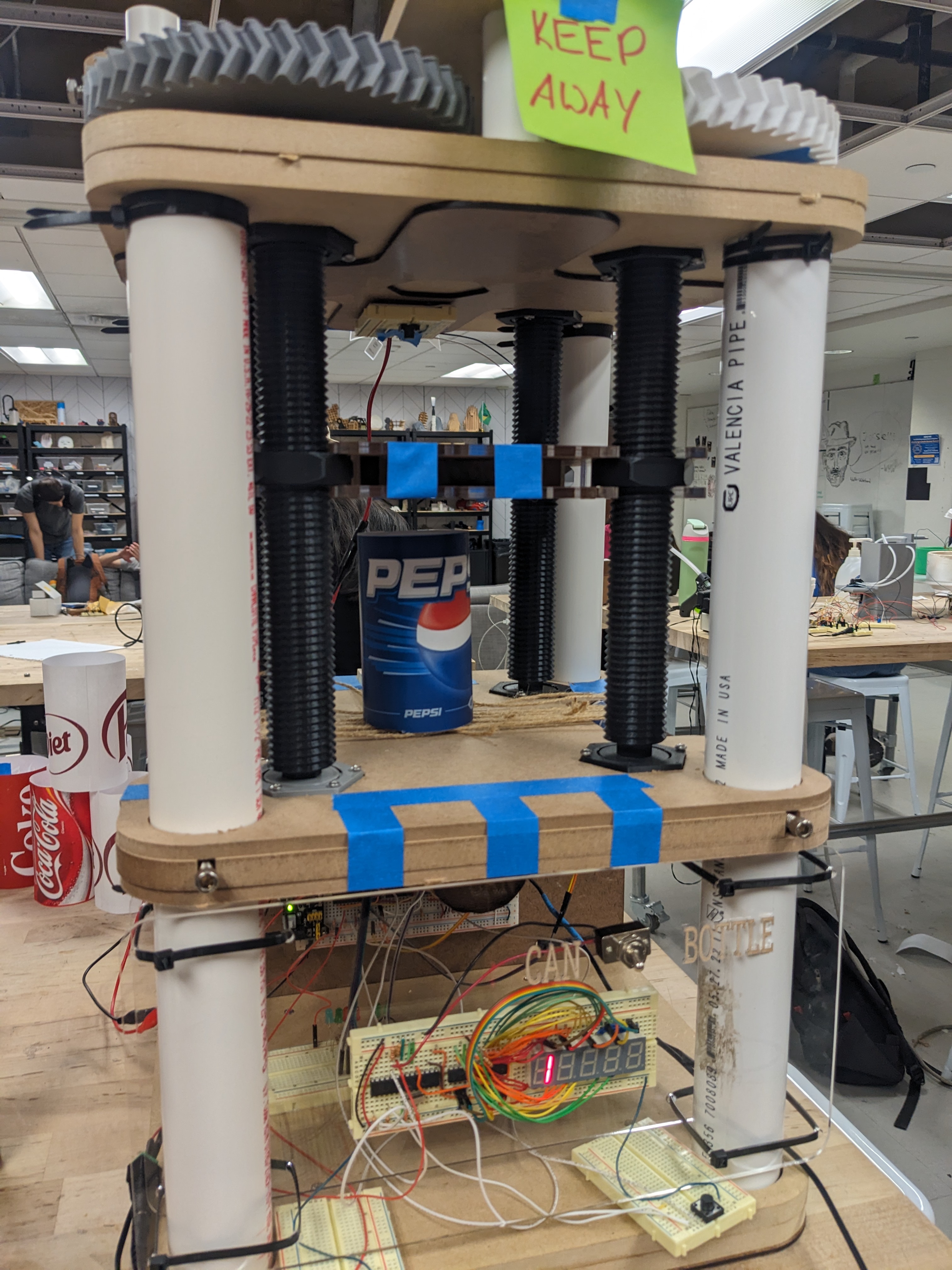
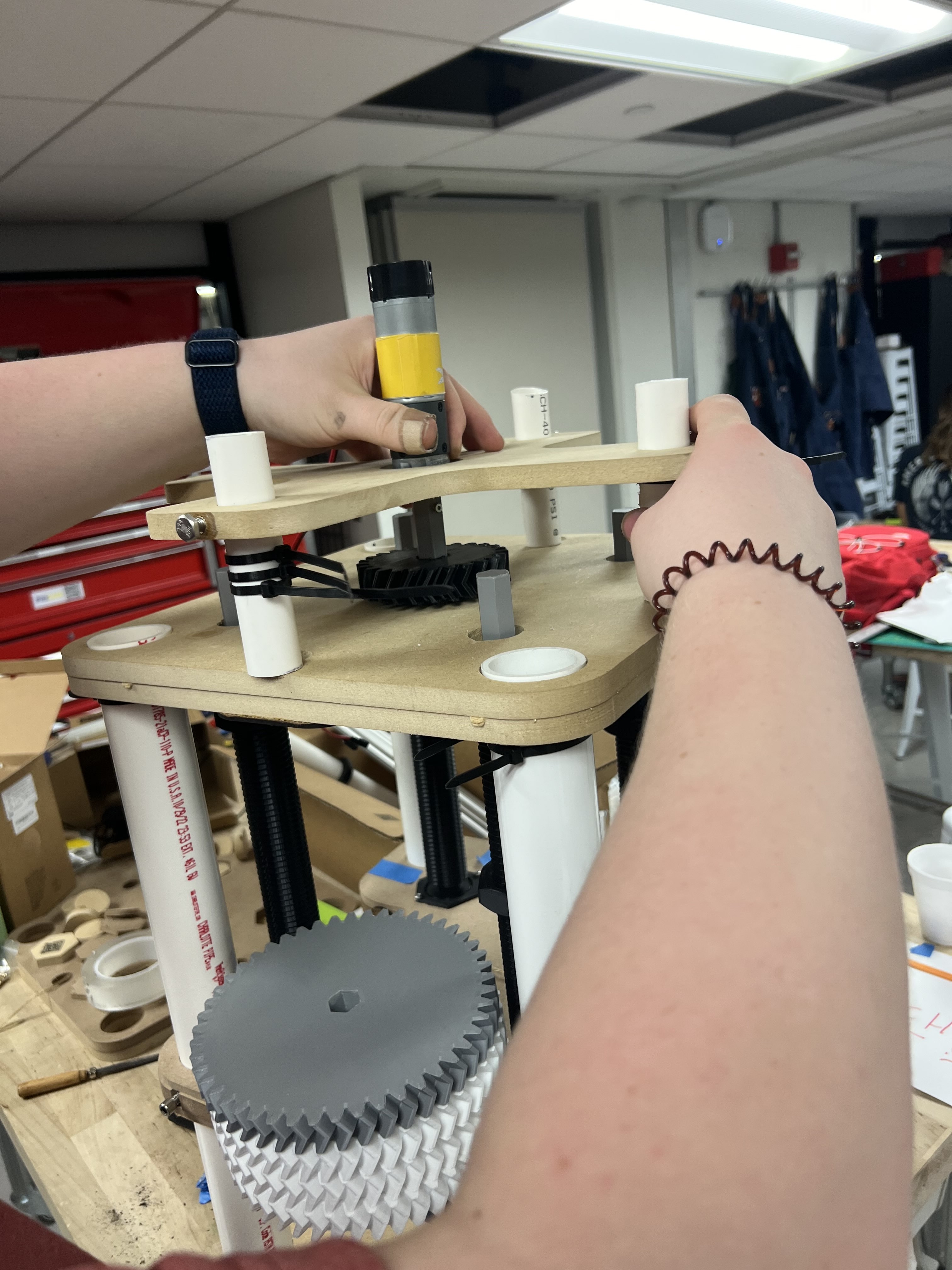
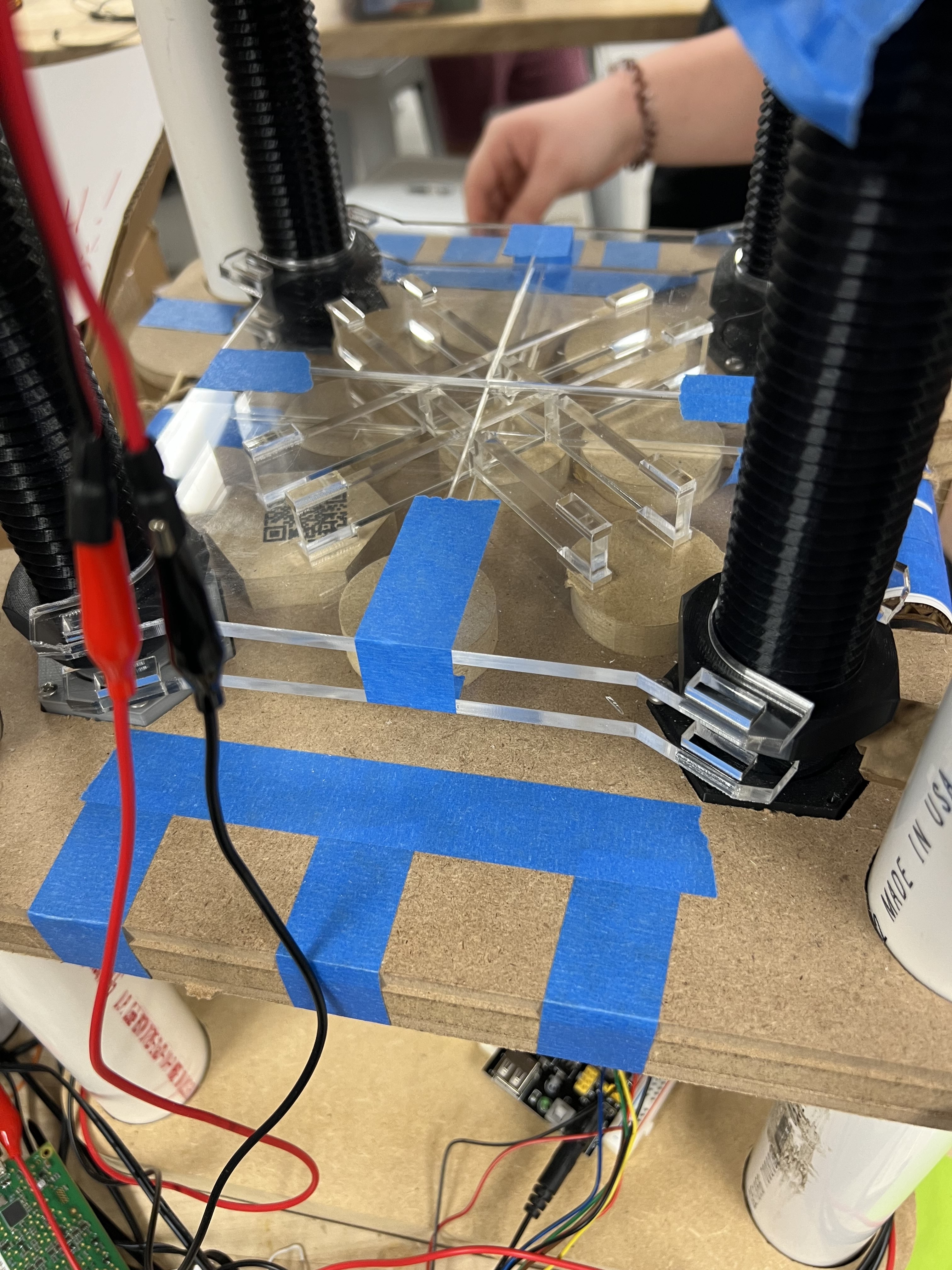
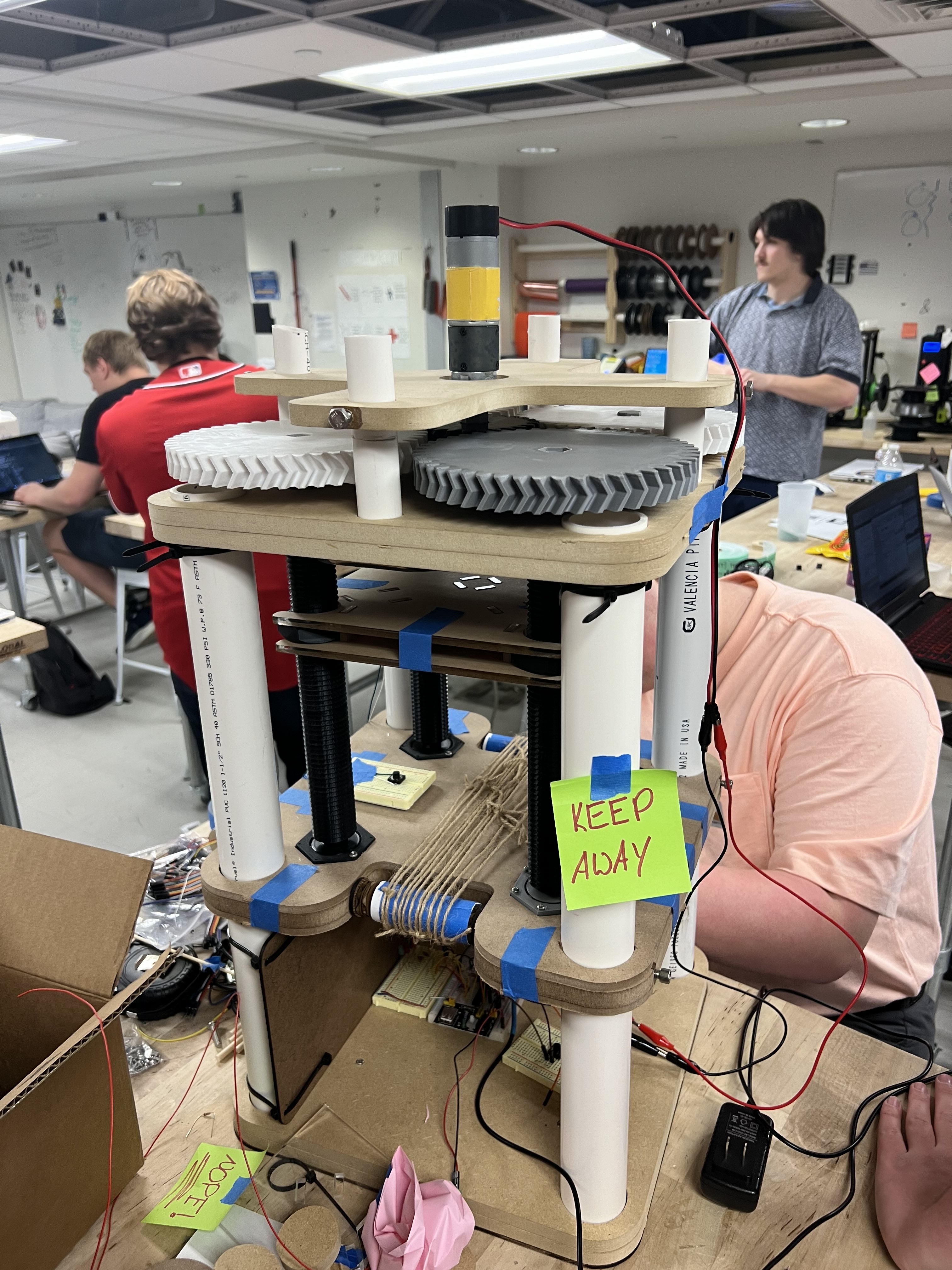
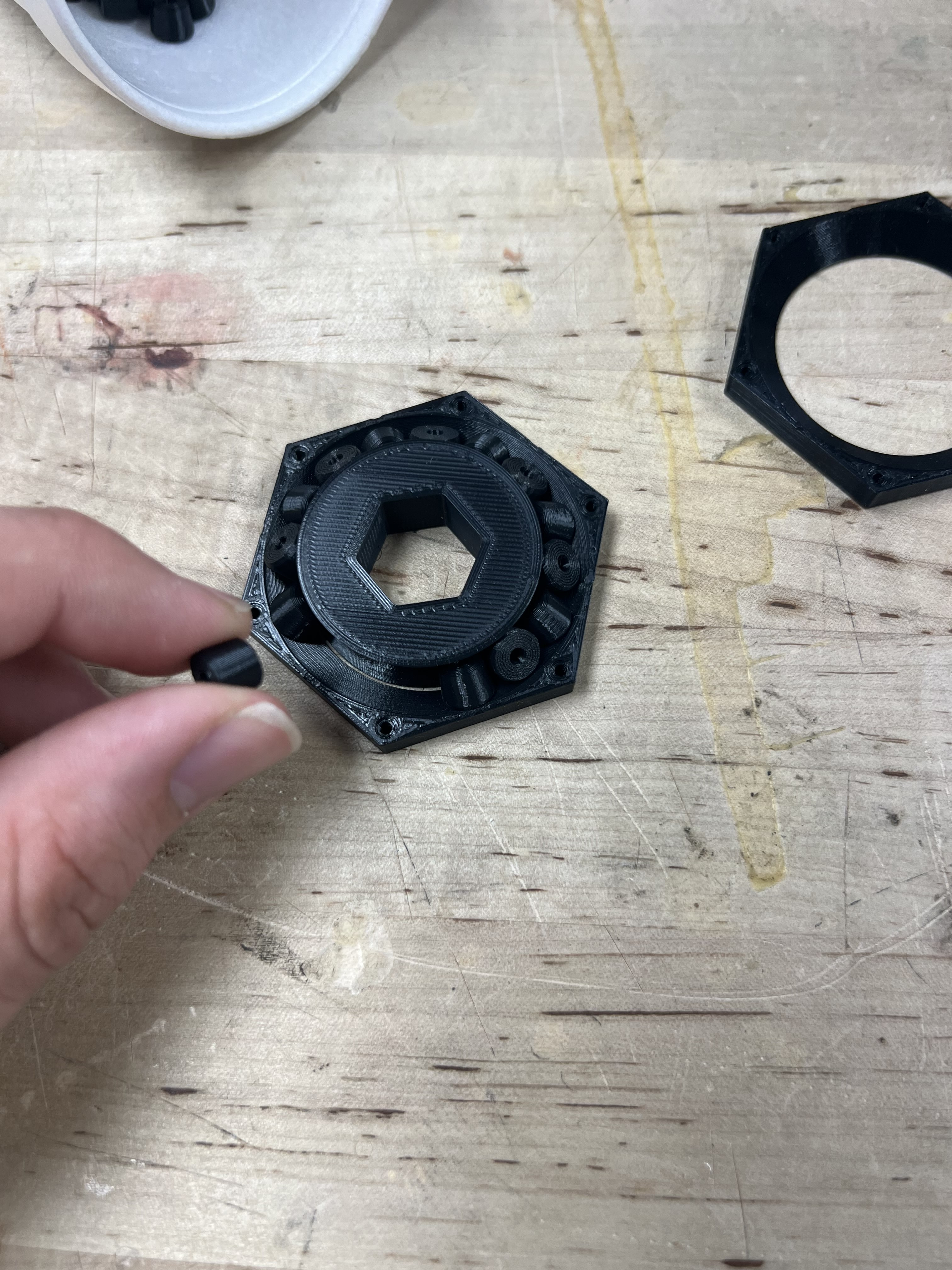